- You are here:
- Homepage
- Components
- Injection Moulding
Silicone Moulding | Experts based in UK
Injection Moulding
A screw injection system in the press provides a specific amount of rubber into a closed, pressurised, mould. The injection unit is fed by a supply of uncured rubber which is maintained at room temperature to prevent premature curing. Because the material is automatically injected into the machine the cycle time (hence cost) of the part is reduced. However, tooling will typically be more expensive due to the engineering of the material flow through the mould.
Large components and components demanding more precision often benefit from being injection moulded. Injection moulding is usually used for multi-cavity moulds and is capable of producing many components per cycle.
This method also allows many of the moulding parameters to be precisely controlled, and as a result injection presses are usually significantly more expensive than a traditional press.
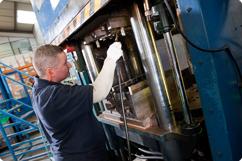
Tight tolerances can often be achieved by altering the flow of material within the mould. We frequently use mould flow simulation techniques to ascertain the optimum mould design. An experienced moulder will save the customer time and money, as the 'de moulding' of the parts can be optimised - hence reducing cycle time and waste parts.